詳情信息
Information

傳統煤粉制備企業是如何清掃粉塵的?
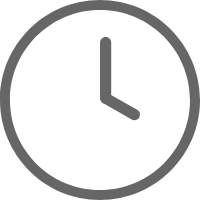
煤粉制備過程屬于物理變化,實質為煤的粒徑和煤中水分的變化。一般原煤的水分大于10%,而煤粉的水分一般要求<6%;對于原煤入磨粒徑而言,一般要求入磨粒徑小于25mm,否則需先經過破碎,遵循“多破少磨”的節能原則,鍋爐燃燒煤粉一般要求粒徑在20~50um之間。在煤粉制備生產過程中工藝控制都是圍繞著煤粉水分和煤粉粒度這兩個指標展開的。
烘干、研磨及輸送構成了制粉過程的三大核心環節,根據烘干形式的不同,制粉工藝可分為一步法和兩步法;根據研磨方式不同,可分為球磨研磨和立式研磨;輸送過程可分為氣力輸送和機械輸送方式。
小編發現在煤粉烘干環節,由于帶式烘干機將煤塊加熱至一定的溫度,使其中水分蒸發,在被皮帶輸送至烘干機外后,與車間溫度形成反差,出現蒸騰現象,一是造成車間升起濃濃迷霧,二是隨著蒸騰現象,部分超細煤粉,也隨之飄入空中,再于空中結露降至地面、設備表面。
但在煤粉烘干環節,車間產生粉塵逸散問題也不是家家都有的,烘干分兩步法(先烘后磨)和一步法(邊烘邊磨),兩步法一般采用帶式烘干機或回轉窯爐對原煤進行烘干,烘干后的物料再進入磨機進行研磨。帶式烘干機一般采用電加熱的方式,不僅耗能大,而且烘干效率偏低,一般來說,烘干后的水分不低于9%;回轉窯爐一般采用煤粉作為燃料進行烘干,但烘干后的原煤水分也不低于7%,難以達到工業煤粉的要求,而且兩次烘干增加了原煤輸送倒運的次數,增加了生產成本。
兩步法無法實現原煤低水分的原因在于,原煤內部空隙發達,對原煤進行直接烘干,原煤內部的游離水和結合水無法得到蒸發。由于采用兩步法在烘干原煤的過程中烘干效率低、耗能大,且無法將原煤水分烘干至5%以下,因此在煤粉制備過程已逐漸棄用。
采用一步法邊烘邊磨的形式具有很大優勢:原煤經過研磨形成煤粉的過程中原煤內部的游離水還有部分結合水會形成水蒸氣而排出,不僅耗能低,而且制備出的煤粉水分低可達3%。此外,水分的降低還會增加物料的可磨性,提升磨機的磨礦效率,因此目前制粉廠普遍采用一步法的方式進行烘干。